The empty plastic bottle bagging machine is a specialized piece of equipment used in PE, PP, PET and other plastic bottle production lines. Its purpose is to automatically put empty bottles into plastic bags, thus facilitating the cleaning and turnover of bottles. This equipment is widely used in the food and pharmaceutical industries. The following article will provide some guidance on how to select the most suitable bagging machine.
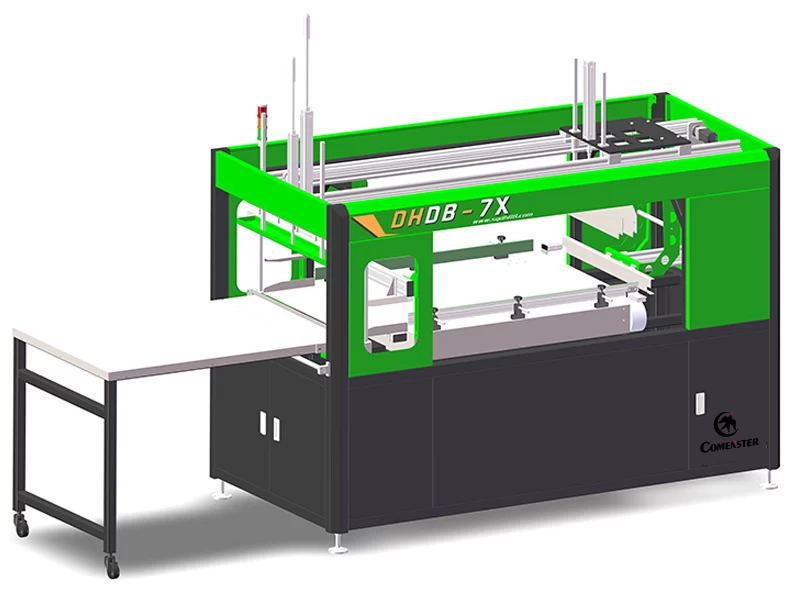
To select the most suitable baler from Comenster Machinery, simply provide the following information:
1. Bottle Type
A. There are several bottle types that a bagging machine can be compatible with. However, the changed parts need to be replaced, including the push plate and bag support mechanism.
B. Bottle shape: square bottles, round bottles, other shape bottles, etc. It is not necessary to arrange square bottles. Round bottles should be arranged as far as possible and packed as compactly as possible. Please confirm with the technical department whether oval bottles, slender bottles, cone bottles, etc. are suitable.
C. Bottle capacity: Different bottle volume is suitable for different models.
2.Packaging specifications
Please provide the seller with the packaging specifications you require. This should include details of the number of rows of each bag, the number of square bottles or large bottles, the number of odd and even rows of round bottles, and any dislocation.

3.Production capacity of bottle blow molding machine
The production capacity of bottle blow molding machine is an important basis for equipment selection. Please inform the seller of the actual production capacity of your bottle blow molding machine, as this will help them select the appropriate bagging machine. The production speed of the bagging machine should be larger than the production speed of the bottle blow molding machine, in order to achieve the perfect packaging effect.
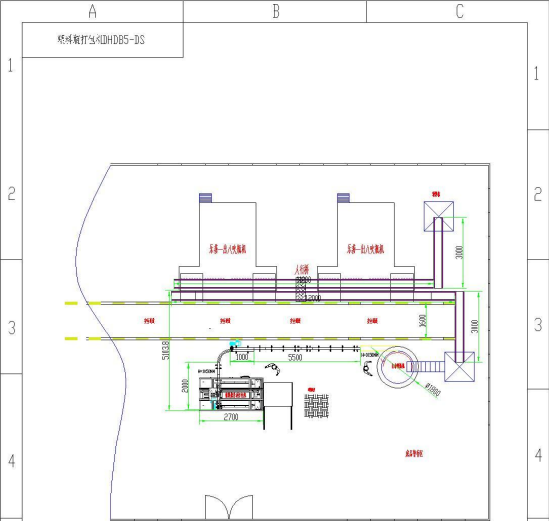
4.Direction of operation and bottle infeed
Due to the changing location of the customer, the bagging machine is set up in the customer's production workshop, and the bottle entering the machine may be left or right; similarly, the operation screen of the machine must also be located according to the location situation, and the two directions should be confirmed before the equipment is made. If space permits, we recommend that the direction of operation is the same as that of the cylinder. When the bagging machine is working, it is more convenient for the operator to operate the equipment.
5. Bagging platform height
The height of the workbench refers to the distance between the arrangement platform and the ground inside the machine. The height of the bottle delivery line, the height of the discharge platform and the bagging height of the workers should be consistent with this height. After years of design experience in our company, 1050mm is the most convenient gold size for operator bags. This height can be customized if required to be consistent with the front end equipment, but the minimum recommendation is not less than 800mm.
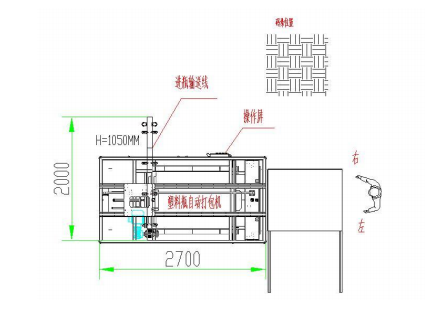
6. Bag Material
There are three types of common bag materials in the market: PE plastic bags, PVC plastic bags, woven bags, PE and PVC plastic bags can be used with hot sealing function, automatic sealing function, woven bag packaging without automatic sealing function. Most customers are using plastic bag packaging, cold and hot sealing knife automatic sealing, sealing close without broken bag.
Finally, you need to determine your own budget. Different bagging machine models have their own characteristics and advantages in different application scenarios and budgets. If the budget is sufficient and the pursuit of automation workshop, you can choose the automatic machine!
The example layout of bagging machine in your factory.